In the dietary supplement manufacturing industry, the choice of raw materials is crucial in determining the final product’s quality and efficacy. This article provides the definition of raw materials, an overview and detailed insights into the critical factors to consider when sourcing custom supplements. From selecting suitable raw materials to understanding the latest industry trends, let’s delve into the key factors and effective strategies for managing material inventory.
Key Takeaways
- Raw materials for dietary supplement production include unprocessed substances such as herbs, powdered vitamins, and minerals.
- Raw materials play a crucial role and are a decisive factor in dietary supplements’ quality, efficacy, and safety.
- Raw materials fall into three categories: Natural Raw Materials, Synthetic Raw Materials, and Processed Raw Materials.
- Consideration of purity, source, and quality standards is essential when choosing raw materials for production.
- Stay updated on future trends in raw materials, such as Sustainable Materials, Technological Innovations, and Circular Economy.
What is Raw Materials?
In the dietary supplement industry, raw materials include herbs, powdered vitamins, plant extracts such as green tea extract, pure minerals like calcium and magnesium, and compounds such as glucosamine. These materials are often used to formulate health-supporting products such as capsules, tablets, powders, or nutritional beverages.
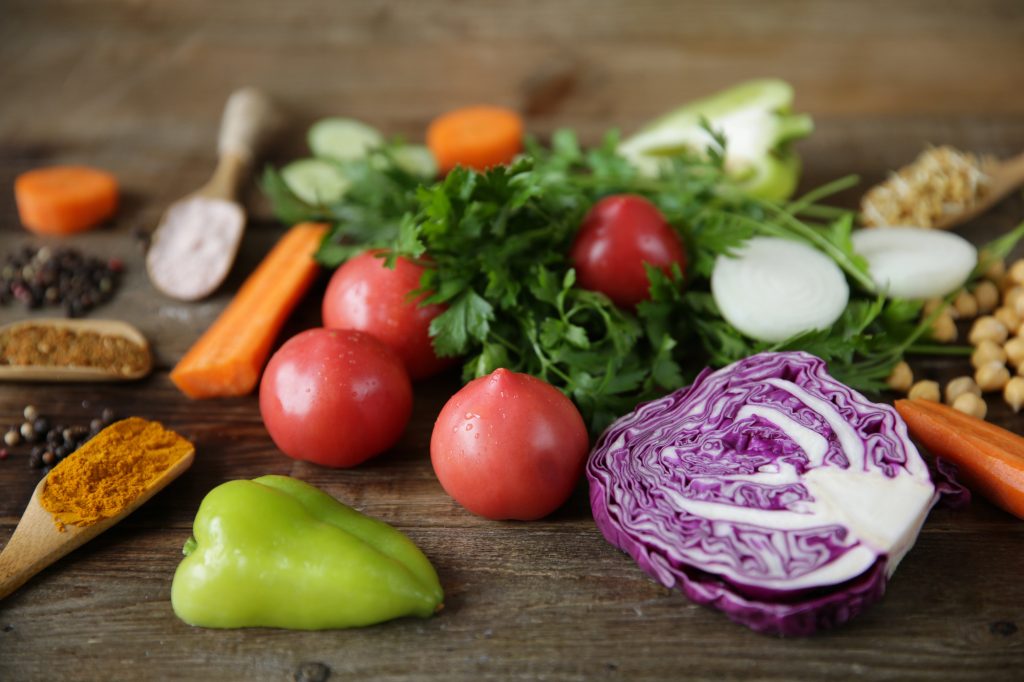
Importance of Raw Materials in Manufacturing
Raw materials for manufacturing are critically important as they form the foundation for each product’s quality, efficacy, and safety. For example, ginseng extract must be carefully selected to ensure the appropriate level of active ingredients, or vitamin C needs to be tested to ensure it is free from harmful contaminants.
Given the direct impact of raw materials on product quality, selecting and handling these materials requires significant effort and precision. Each manufacturer needs to learn how to identify high-quality raw materials and hold them to minimize health risks and enhance consumer trust in the product.
Direct vs. Indirect Raw Materials
Understanding the difference between direct and indirect raw materials is essential for creating compelling product formulations. This knowledge optimizes the manufacturing formula and ensures the quality and safety of health supplements.
Direct Raw Materials
Direct raw materials are the primary components that directly contribute to the final product’s efficacy. They are included in the product formula without undergoing additional transformation.
For example, powdered or tablet collagen is a direct raw material in a collagen supplement formula, providing essential nutrients for skin repair and regeneration. In a multivitamin supplement formula, pure vitamins and minerals like vitamin C, B12, and calcium are crucial in supplying necessary nutrients to the body.
Indirect Raw Materials
Indirect raw materials do not directly contribute to the final product’s structure but play a supportive role in the manufacturing process or improve the product’s properties. Stabilizers, additives, and colorants are typical examples.
Similarly, binders or preservatives in tablet supplement production help maintain the tablet’s shape and stability during storage. They do not provide direct health benefits but ensure that the final product remains stable and convenient.
Types of Raw Materials
The list of raw materials for manufacturing includes three main types: natural, synthetic, and processed. Every raw material used in production plays a specific role and directly impacts the final product.
Natural Raw Materials
Natural raw materials are components extracted directly from natural sources without undergoing chemical synthesis.
Example: In dietary supplements, herbs such as Tongkat Ali and Ginseng are commonly used as natural raw materials for supporting health and boosting energy. Vitamins and minerals like vitamins A, C, and zinc are also necessary natural raw materials, providing nutritional benefits to the body.
Synthetic Raw Materials
Synthetic raw materials are produced through chemical processes to create specific components.
Example: Some supplements contain synthetic vitamin D or amino acids to enhance nutrition. These materials are often designed to provide a precise amount of essential nutrients. They can be adjusted to meet the specific needs of each product formulation.
Processed Raw Materials
Processed raw materials are components that have undergone some processing before being used in production.
Example: Collagen powder and probiotics (beneficial bacteria) are processed ingredients refined to dissolve and absorb more easily. Supporting additives like preservatives, binders, and anti-caking agents also fall into the category of processed raw materials.
Selection Process and Origin of Raw Materials
To choose the right quality of raw materials to ensure the quality and effectiveness of the final product, consider the following essential factors:
- Origin of Raw Materials
They can come from various sources, including plant, animal, and synthetic origins. Assess the needs of the supplement formula and select appropriate sources of raw materials.
- Quality Requirements and Standards
You need to consider the consistency of quality and stability of the material throughout its shelf life. Raw materials must meet standards for contamination levels and be free from harmful substances or impurities. The origin of raw materials should be verified to ensure their safety and sustainability.
- Purity and Bioavailability
Raw materials should be refined to remove impurities and unwanted compounds, ensuring purity suitable for processing. Additionally, bioavailability—the extent to which the body can absorb and utilize nutrients from the material—should be considered. Higher bioavailability will provide better effectiveness for the supplement formula.
- FDA, GMP, and Other Certifications
Selected raw materials must comply with the Food and Drug Administration (FDA) regulations and be produced and processed according to Good Manufacturing Practices (GMP). Additionally, you may evaluate the quality of raw materials based on other certifications, including organic, non-GMO, and reputable international certifications.
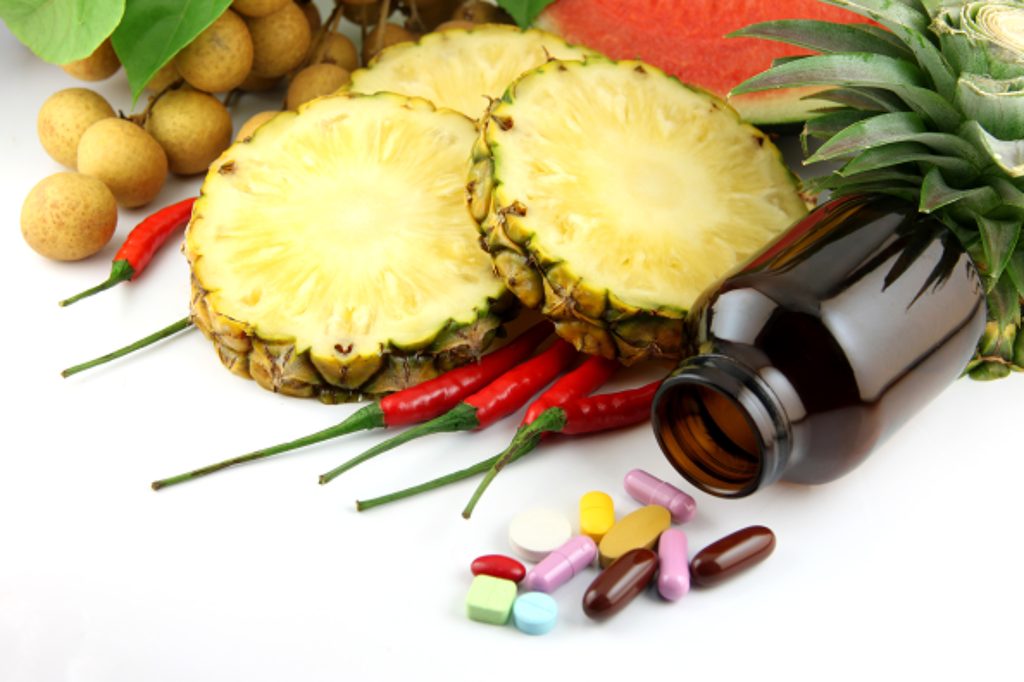
The Formula For Using Raw Materials In Dietary Supplement Production
Once the appropriate raw materials are selected, formulating their use accurately is also crucial to ensure product quality.
Steps for Selecting Ingredients for Each Type of Supplement
Each type of dietary supplement has specific raw material requirements. The following steps will help you choose the appropriate ingredients:
- Determine the product’s objective: For products aimed at improving skin health, you might need ingredients like collagen, or vitamin C. Consider adding natural herbs like Tongkat Ali or Ginseng for overall health support.
- Choose high-quality raw materials: Ensure that input materials always meet quality and health safety standards.
- Experiment and optimize: Test multiple formulas, then learn and optimize to finalize the formula. This step will help save costs and effort in the long run.
The Role of Ingredient Ratios in the Production Formula
The ratio of raw materials used in the production formula dramatically impacts the effectiveness and stability of the final product. An appropriate ratio helps balance nutrients and optimize product benefits while minimizing undesirable side effects and extending product shelf life.
Combining and Adjusting Raw Materials
After selecting ingredients based on the product’s goals, adjust the percentage ratio of each component to ensure balance and effectiveness. Consider two main issues:
- Compatibility: Raw materials need to be compatible with each other to avoid adverse effects or reduced effectiveness.
- Overall Effectiveness: Adjust the ratios so that each ingredient delivers maximum effectiveness without compromising product quality.
Difference Between Raw Materials And Processed Materials
Criteria | Raw Materials | Processed Materials |
Definition | Raw materials are components in their natural, unprocessed state, often requiring further refinement. | Processed ingredients have undergone processing or treatment before use. |
Purity Level | Typically in a natural state, may contain impurities or require additional purification. | Processed to achieve higher purity, with impurities removed during processing. |
Stability | May be unstable, prone to degradation or changes over time. | Generally more stable and have a longer shelf life due to processing. |
Safety | May require thorough quality and safety checks due to lack of processing. | Processed and tested to ensure safety and meet quality standards. |
Application in Production | Requires additional processing steps to become a final product, potentially variable in quality. | Ready for use in production, reducing time and effort in the processing stage. |
Examples | Herbal powders, raw plant extracts, unprocessed natural ingredients. | Vitamin capsules, refined extracts, processed collagen powders. |
Difference Between Inventory And Raw Materials
Criteria | Raw Materials | Inventory Materials |
Definition | Raw materials are components in their natural, unprocessed state, often requiring further refinement. | Inventory includes products or materials that are stored for future use or distribution. |
Condition | In an unfinished state, requiring additional processing before use in production. | Processed or completed, ready for inclusion in the production process or distribution. |
Usage | Used as the initial input in the production of dietary supplements. | Can include processed ingredients, finished goods, or semi-finished products awaiting shipment. |
Processing | Must undergo various stages of processing and quality checks before use. | Has completed processing stages, may require periodic quality checks and warehouse maintenance. |
Examples | Herbal powders, raw plant extracts, unprocessed natural ingredients. | Finished vitamin capsules, processed extract powders, packaged supplements ready for sale. |
How Are Raw Materials Different From Sub-Assemblies?
Criteria | Raw Materials | Sub-Assemblies |
Definition | Raw materials are components in their natural, unprocessed state, often requiring further refinement. | Sub-assemblies are partially completed products or components that are assembled before final production. |
Condition | In their natural, unprocessed state, requiring further processing to be used in the final product. | Partially processed or assembled, often consisting of multiple raw materials combined into a component. |
Usage | Serve as the foundational inputs for manufacturing dietary supplements. | Act as intermediary products that are integrated into the final product during the production process. |
Processing | Requires initial processing or refinement before it can be used in manufacturing. | Often involves additional assembly and integration of various components before final assembly. |
Complexity | Generally simple and single-component, needing significant processing to become part of the final product. | More complex, consisting of multiple components or raw materials that have been partially assembled. |
Examples | Herbal powders, raw plant extracts, unprocessed natural ingredients. | Pre-assembled capsules, blended powders, or premixed formulations ready for final processing. |
Key Factors to Consider When Choosing Raw Materials
The key factors to consider when selecting suitable raw materials for the dietary supplement industry include:
- Quality and Purity: The raw materials must meet standards for purity and should be free from contaminants or harmful compounds.
- Bioavailability: Assess the body’s ability to absorb and utilize the raw materials’ nutrients effectively.
- Regulatory Compliance: Raw materials should meet the Food and Drug Administration (FDA) regulations, adhere to Good Manufacturing Practices (GMP), and comply with other international certifications.
- Stability and Storage: Choose raw materials with appropriate storage requirements to prevent spoilage and extend shelf life.
- Cost and Economic Efficiency: Consider the cost of raw materials to ensure they fit within the production budget and do not excessively increase the product price. Compare prices from various suppliers to optimize costs.
- Origin and Sustainability: The source of the raw materials and sustainability in the production process are increasingly important. Materials should be harvested or produced using sustainable and environmentally responsible methods.
Sourcing Strategies for Manufacturers
The raw material supply chain for the dietary supplement industry requires a deep understanding of the market and frequent updates to make informed decisions. First, a company needs to decide whether to use domestic or international suppliers:
Local Sourcing
- Advantages:
- Proximity and more accessible control: Raw materials supplied close to the production site allow for more straightforward quality checks and supply control.
- Reduced shipping costs: Domestic sourcing lowers shipping costs and risks associated with international delivery.
- Disadvantages:
- Limited options: Finding high-quality or specialized raw materials may be challenging.
- Higher costs: Domestic raw materials may be more expensive due to higher production costs.
Global Sourcing
- Advantages:
- Diverse options: Access a wider variety of high-quality raw materials from international suppliers.
- Competitive pricing: Lower production costs due to large-scale production and lower labor costs in other countries.
- Access to special materials: The ability to source unique or rare raw materials unavailable domestically.
- Disadvantages:
- Shipping risks: International shipping can involve risks, longer delivery times, and higher shipping costs.
- Quality control challenges: It is harder to verify the quality of raw materials from a distance, increasing the risk of substandard quality.
The next step is to develop a supply chain management system to ensure continuous supply and build long-term relationships with suppliers to maintain material quality. Companies should regularly forecast demand, manage inventory, and assess risks. Additionally, maintain frequent communication, negotiate mutually beneficial agreements, and provide timely, constructive feedback to suppliers to encourage improvement.
Future Trends in Raw Material Usage
Manufacturers should focus on current raw material sourcing and consider future trends to meet technological advancements and environmental sustainability requirements. Key future trends in raw material usage include:
- Sustainable Materials:
- Renewable Resources: Increasing preference for raw materials from renewable resources like plants or sustainable agriculture. For example, using organic soy protein powder or algae helps reduce pressure on natural resources.
- Recycling and Waste Reduction: The industry actively seeks solutions to recycle raw materials or minimize waste. Using recycled raw materials like fruit peel powders helps reduce waste and optimize resource use.
- Technological Innovations:
- Nano Materials: Nanotechnology improves raw material properties, such as enhancing absorption or biodegradability. Nano-sized particles can increase the effectiveness of nutrients in dietary supplements.
- Bio-based Materials: Raw materials from biological sources, such as bio-polymers or extracts from microorganisms, are becoming attractive. These materials are not only environmentally friendly but may also offer unique nutritional benefits.
- Circular Economy:
- Material Reuse: Implementing methods to reuse raw materials can help reduce the need for new resources. For example, by-products from production processes can be recovered and recycled into materials for other products.
- Sustainable Design: The industry increasingly focuses on designing products and production processes that facilitate easy recycling or reuse of materials, aiming to minimize environmental impact and reduce production costs.
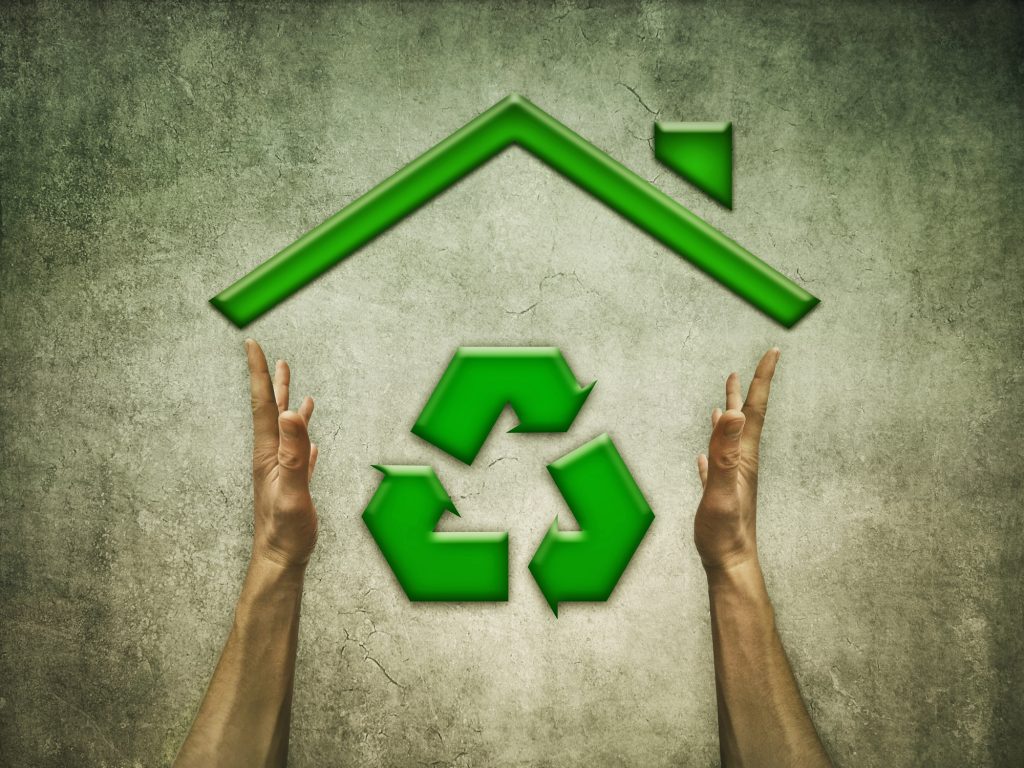
FAQs
Is Water a Raw Material?
Yes, water is a raw material; it is commonly used as an essential ingredient in food processing. Water plays a role in dissolving other ingredients in the functional food industry.
Do Manufacturers Use Raw Materials?
Yes, manufacturers need to use raw materials in the production process to create the final product. These materials directly impact the quality of dietary supplements and the consumer’s health.
How Are Raw Materials Used In The Production Formula?
Raw materials are selected based on quality and functionality, then measured and blended according to specific ratios based on the production formula. Raw materials such as grinding, dissolving, heat treating, packaged, stored, and used in production must be processed.
Who Provides Raw Materials To Manufacturers?
Manufacturers can purchase raw materials from raw material processing companies, distributors from various sources, and specialized suppliers in the functional food industry.
Conclusion
Understanding raw materials and their impact on the final product is crucial in the dietary supplement manufacturing industry. Robinson Pharma Inc and other manufacturers can optimize their production processes, ensure product quality, and meet market demands by applying knowledge about material selection, supply chain management, and new trends like sustainable materials and advanced technologies. We hope this information has helped achieve sustainable success in the dietary supplement industry.